First, it is important to understand that the primary goal of a quality process should be to identify and correct issues at the process level that are impacting performance. However, most quality programs focus almost exclusively on agent issues, which is incorrect.
Quality data can and should drive positive change among agents handling customer transactions. Aggregate, analyze and pass this data to the operational management team for coaching opportunities. However, identifying and addressing process-level issues can lead to significant improvements and positive changes.
Here are steps to help you systematically identify and address process-level issues:
1. Map Out the Current Processes
- Document Each Step: Create a detailed flowchart or process map that outlines each step of the current QA processes.
- Identify Key Touchpoints: Highlight critical points where errors or issues commonly arise.
2. Collect and Analyze Data
- Gather Data: Collect data on process performance, including error rates, turnaround times, and customer feedback.
- Use KPIs: Identify key performance indicators (KPIs) relevant to the process and track them over time.
- Analyze Trends: Look for patterns and trends in the data to pinpoint where problems occur most frequently.
3. Conduct Root Cause Analysis
- Identify Root Causes: Use techniques such as the 5 Whys, fishbone diagrams, or Pareto analysis to determine the root causes of issues.
- Involve Stakeholders: Engage team members involved in the process to get their insights and perspectives.
4. Implement Process Improvements
- Redesign Processes: Based on the root cause analysis, redesign the processes to eliminate inefficiencies and errors.
- Standardize Procedures: Develop standard operating procedures (SOPs) to ensure process consistency and clarity.
- Automate Where Possible: Use automation tools to streamline repetitive tasks and reduce human error.
5. Monitor and Adjust
- Continuous Monitoring: Regularly monitor the updated processes to ensure they are working as intended.
- Feedback Loops: Establish feedback loops to gather input from employees and customers about the new processes.
- Make Adjustments: Be prepared to make further adjustments based on the feedback and ongoing data analysis.
6. Train and Communicate
- Employee Training: Provide comprehensive training to employees on the new processes and tools.
- Clear Communication: Ensure clear and consistent communication about process changes and their reasons.
7. Review and Refine
- Periodic Reviews: Conduct regular reviews of the QA processes to identify any new issues or areas for improvement.
- Stay Updated: Keep abreast of industry best practices and incorporate them into your QA processes.
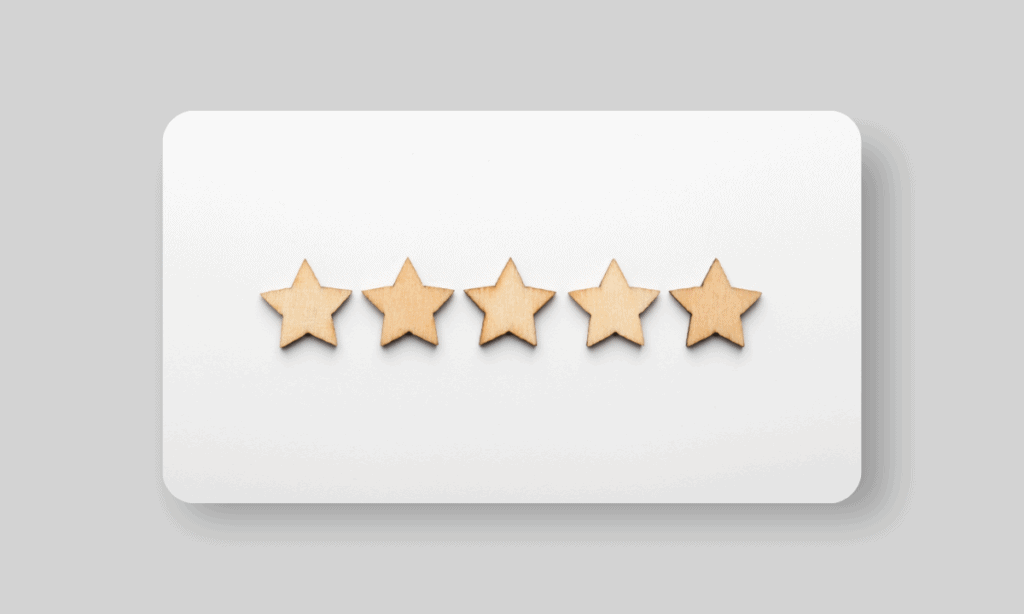
Related: White Paper
How to Design Quality to Link
to Customer Satisfaction
Learn the seven fundamental changes we recommend to clients to drive improvements in their quality program.
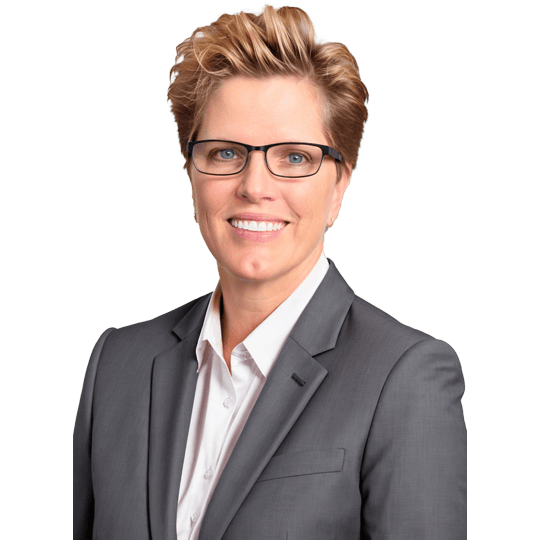
Judi Bolden, Vice President at COPC Inc., brings over 30 years of expertise in performance improvement, operational management, and change management. At Groupon, she led significant enhancements in global support and vendor operations, boosting customer satisfaction and operational efficiency.
Judi is a sought-after speaker with an MBA from Houston Baptist University and a Lean Six Sigma Master Black Belt. Her leadership spans 36 countries, where she’s renowned for her practical solutions to enhancing contact center operations and training.